Quality control
Initiatives through business activities
We are working on quality control and BCP measures to ensure a stable supply of pharmaceuticals.
Quality control
◆ We have acquired international standards for quality control.
The Logistics Division of TOHO PHARMACEUTICAL has acquired ISO 9001:2015 certification (an international standard for quality management systems for products and services) and conducts quality control (certification scope: TBC DynaBASE, TBC Hanshin, TBC Saitama and TBC Hiroshima). In addition, TBC Saitama, TBC Hiroshima and TBC DynaBASE have established logistics systems that comply with Good Distribution Practice (GDP) Guidelines for pharmaceuticals, and are working to further strengthen them.
◆ We have established an advanced temperature control system.
We have established optimal distribution temperature control systems according to the temperature zones of pharmaceuticals. With regard to specialty pharmaceuticals that require strict temperature control, use of the constant-temperature transportation device SALM allows specialty pharmaceuticals to be stored in hospitals and clinics after delivery from distribution centers with no need for repackaging. Since the temperature in the box is recorded continuously for more than one month, the quality is ensured, and thus the economical use of the pharmaceuticals can be achieved.
◆ We are committed to medical safety and quality control at pharmacies.
We have established an audit structure using machines, including the introduction of an audit system. In addition, in order to promote drug therapy appropriately and safely, and to bring human errors as close as possible to zero, we report and share our experiences of near misses that very nearly caused an accident. By analyzing these cases and implementing solutions, we are trying to reduce the causes of accidents themselves and improve medical safety. PHARMA MIRAI is conducting more extensive research in collaboration with the University of Tokyo.
◆ We are supplying high-quality generic drugs.
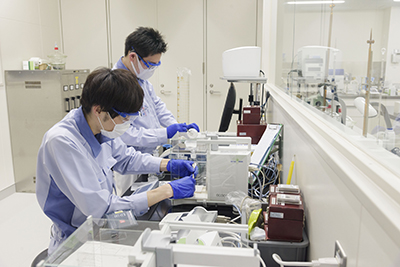
Business Continuity Plan (BCP)
We have established BCP to prepare for natural disasters.
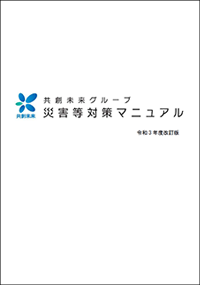
・Redundant host computer and warehouse management system
・Formulation of the Kyoso Mirai Group Disaster Countermeasures Manual (revised in 2021)
・Establishment of the Kyoso Mirai Group Disaster Countermeasures Committee and holding of meetings regularly
・Installation of in-house power generation facilities
・Deployment of emergency bikes
・Installation of disaster priority phones, satellite phones, etc.
・Use of advance notification system for emergency vehicles, etc.
・Introduction of safety confirmation system, etc.